Eine virtuelle Prozesskette soll die Grundlage für eine wirtschaftliche und ressourcenschonende Herstellung von Faserverbund-Preformen für den Großserieneinsatz schaffen. Im Rahmen eines öffentlich geförderten Verbundprojektes entwickelt ein Partnerkonsortium unter Koordination der Neue Materialen Bayreuth GmbH (NMB) eine maschinenunabhängige Software zur virtuellen Abbildung von Legeprozessen für unidirektional verstärkte, thermoplastische Tapes.
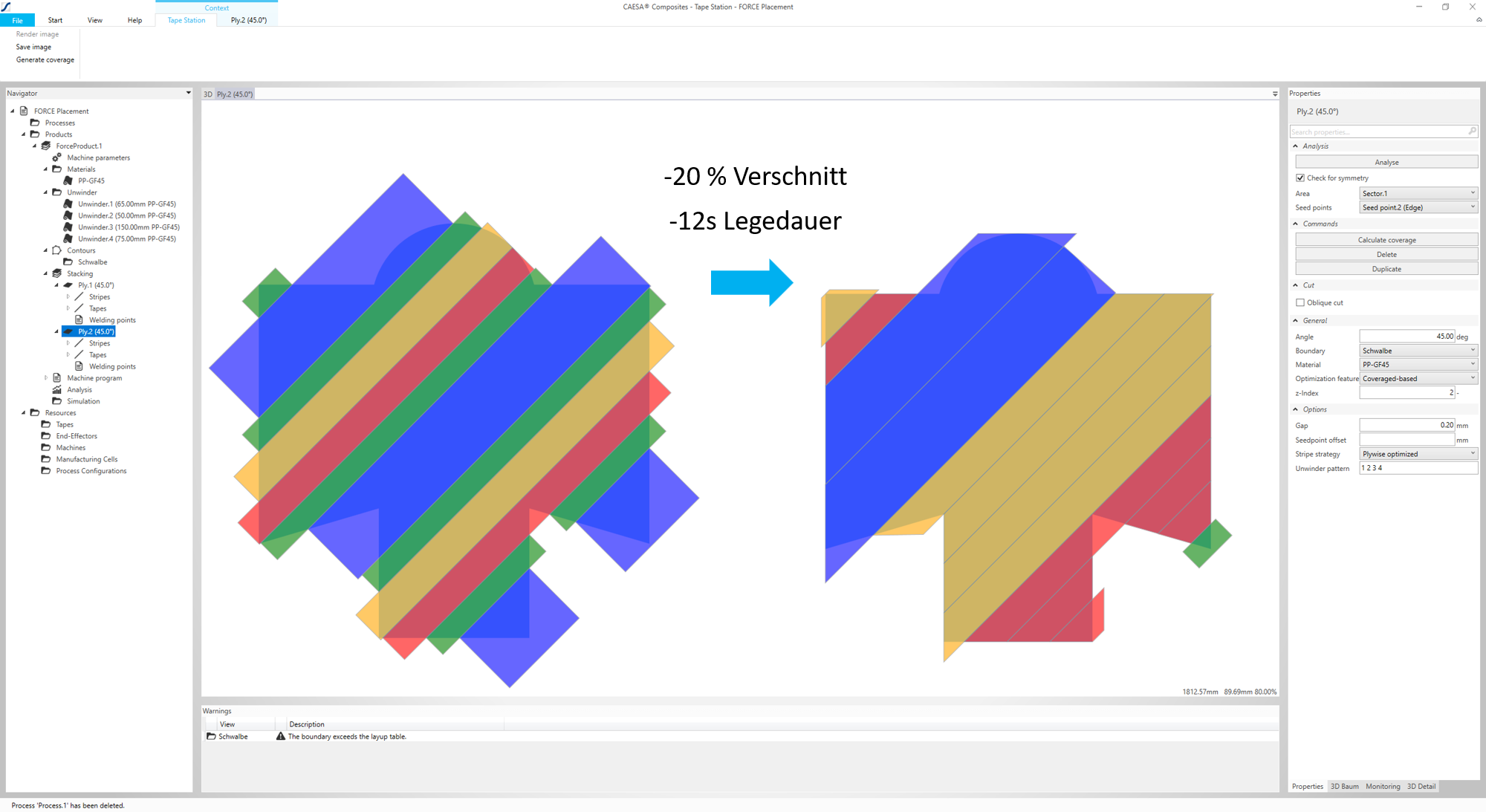
Thermoplastische Faserverbundkunststoffe basierend auf UD-Tapes weisen ein außerordentliches Leichtbaupotenzial auf und sind aufgrund der erreichbaren kurzen Prozesszeiten für den Einsatz in Großserien prädestiniert. Für die Herstellung von maßgeschneiderten Laminaten aus diesen Halbzeugen fehlen aktuell jedoch wirtschaftliche Legeprozesse, die eine virtuelle Prozessumgebung inklusive Optimierungsalgorithmen enthalten. Optimierungen sind hinsichtlich der Legekosten und Verschnitt nötig, weshalb die Technologie bisher nicht den Einsatz für Serienbauteile im Automobilbau gefunden hat.
Im Rahmen des im Zentralen Innovationsprogramm Mittelstand (ZIM) des BMWi geförderten Forschungsprojektes „OptiTape“ entwickeln die Partner SWMS Systemtechnik Ingenieurgesellschaft mbH, Rehau AG + Co und die Forschungseinrichtung Neue Materialien Bayreuth GmbH eine virtuelle Prozessumgebung, die die Identifizierung optimaler Legestrategien für UD-Stacks im Hinblick auf minimalen Verschnitt und Zykluszeit ermöglicht. Diese Software generiert unter Berücksichtigung verschiedener Eingangsgrößen, wie Tapebreiten, Material und Bauteilgeometrie, einen hinsichtlich Kosten, Verschnitt und/oder Legezeit optimierten Gelegeaufbau. Die Arbeiten schaffen damit eine Voraussetzung für eine wirtschaftliche und ressourcenschonende Herstellung von Faserverbundbauteilen im Großserienmaßstab.
Die hohe Zahl an unterschiedlichen Eingangsgrößen machen die Lösung im Hinblick auf Kosten- und Verschnittminimierung zu einem komplexen mathematischen Optimierungsproblem, das mit smarten Algorithmen gelöst werden muss. Damit diese Berechnungen in ein Umfeld einer stabilen und hochautomatisierten Großserienfertigung übertragen werden können, ist die Kopplung von digitaler und virtueller Arbeitsumgebung zwingend erforderlich.
Zusätzlich werden bei der softwareseitigen Optimierung werkstoffwissenschaftliche Rahmenbedingungen, wie der Einfluss von legeinduzierten Spalten und Schweißpunkten auf die mechanischen Eigenschaften des Endbauteils, berücksichtigt. Daher werden diese werkstoffseitigen Kenntnisse über zulässige Defekte und deren Auswirkungen auf die Eigenschaften des Bauteils in Grundlagenuntersuchungen im Rahmen des Vorhabens erarbeitet. Die Erprobung der Software und die Kopplung mit der realen Anlagentechnik werden an der Tapelegeanlage FORCE-Placement der Neuen Materialien Bayreuth GmbH durchgeführt.
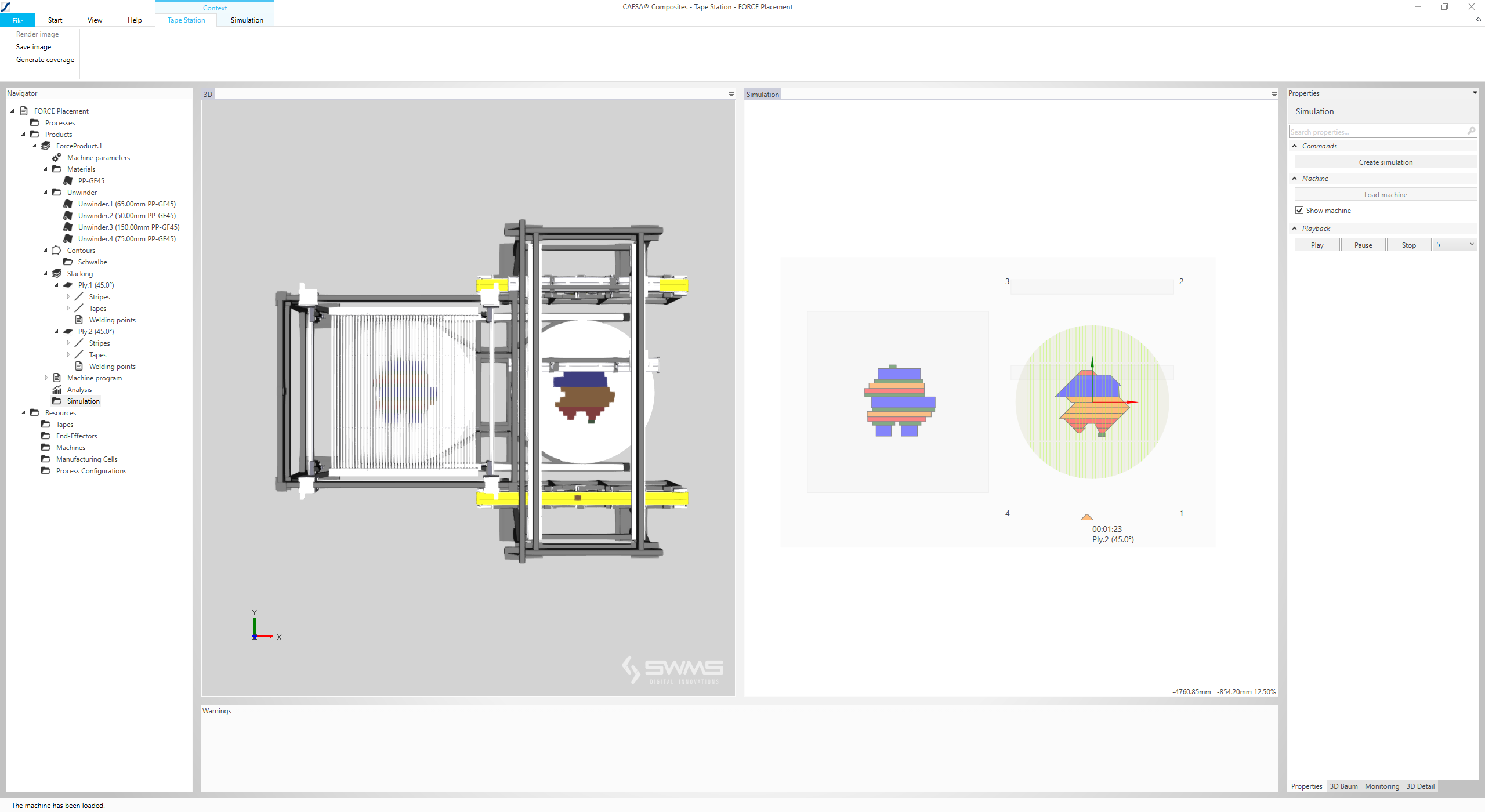
Ansprechpartner
Neue Materialien Bayreuth GmbH
M.Sc. Franz Habla | E-Mail: franz.habla@nmbgmbh.de